Продолжаем наш ежеквартальный DIY Челлендж (#1, #2, #3,#4,#5,#6) где вы можете показывать свои творения и получать за это лайки, фанатов, почет и ачивки! Кстати, у нас уже появился первый обладатель ачивки второго уровня — @arsentiev.
Ачивки есть трех уровней крутости и выдаются за количество самоделок, сделанных по формату: за первую, четвертую и восьмую.
Правила для получения ачивок:
- Тема может быть любой
- Это должен быть полноценный проект, не мелкая самоделка на 15 минут
- Коммент должен быть оформлен по шаблону: с подробным описанием процесса, результатом и советами для других
- Хотя бы на одной фотографии обязательно должен быть крестик Клуба ✖️ и ваш ник на бумажке или иным способом
- Ачивки раздаются в конце квартала
Челлендж продолжается с 1 июля по 1 октября 2024
Заходите с вопросами и за советами в наш DIY чатик!
## Самоделка: ХХХ
## Фото результата 1-2
## Описание процесса с фото 2-3
## Tips&tricks (ваши советы для других)
Мой календарь забыл мне напомнить подвести итоги, так что подвожу с опозданием в месяц. Но хочу сказать, что этот челлендж получился особенно мощным, всем большие респекты, такие штуки очень мотивируют идти и делать что-то самому!
Всем участникам выдам ачивки, вы крутые!
PS на всякий случай напоминаю, что у нас аж три уровня ачивки! Если у вас вдруг набралось уже достаточно на новую ачивку, а я не выдал, напишите мне в личку плз.
Ламповая лампа
Это пожалуй мой самый долгий и дорогой DIY проект, и я так рад что довёл его до конца не бросив!
Началось всё с того что у меня была лампа со сломанным абажуром, думал что бы с ней сделать. Тут мне на глаза попалась скульптура Steven Shearer. Ну какая красота, хочу так!
Фото результата
Результатом я очень доволен - я заранее знал что медь потемнеет и я не хотел такого глянцевого галерейного вида как у Стивена.
Через пару месяцев она станет немного зелёной и будет совсем винтаж/стимпанк.
Описание процесса
У меня уже был опыт паяния медных труб, поэтому я без особого плана отправился в строительный за 15мм трубами. В этом была главная ошибка - я ошибся с трудозатратах и материалах примерно в 5 раз. 😱
Чистого времени ушло 8 полных дней (70-80 часов) и примерно €400 только на материалы. На пайку ушла целая 600мл банка пропана.
Если кто-то захочет такое повторить - смоделируйте сначала всё в каде.
Первой проблемой было придумать как прикрепить будущую конструкцию к ножкам. Я спаял длинную трубку, и развел трубки в стороны чтобы получить базовый квадрат-основание
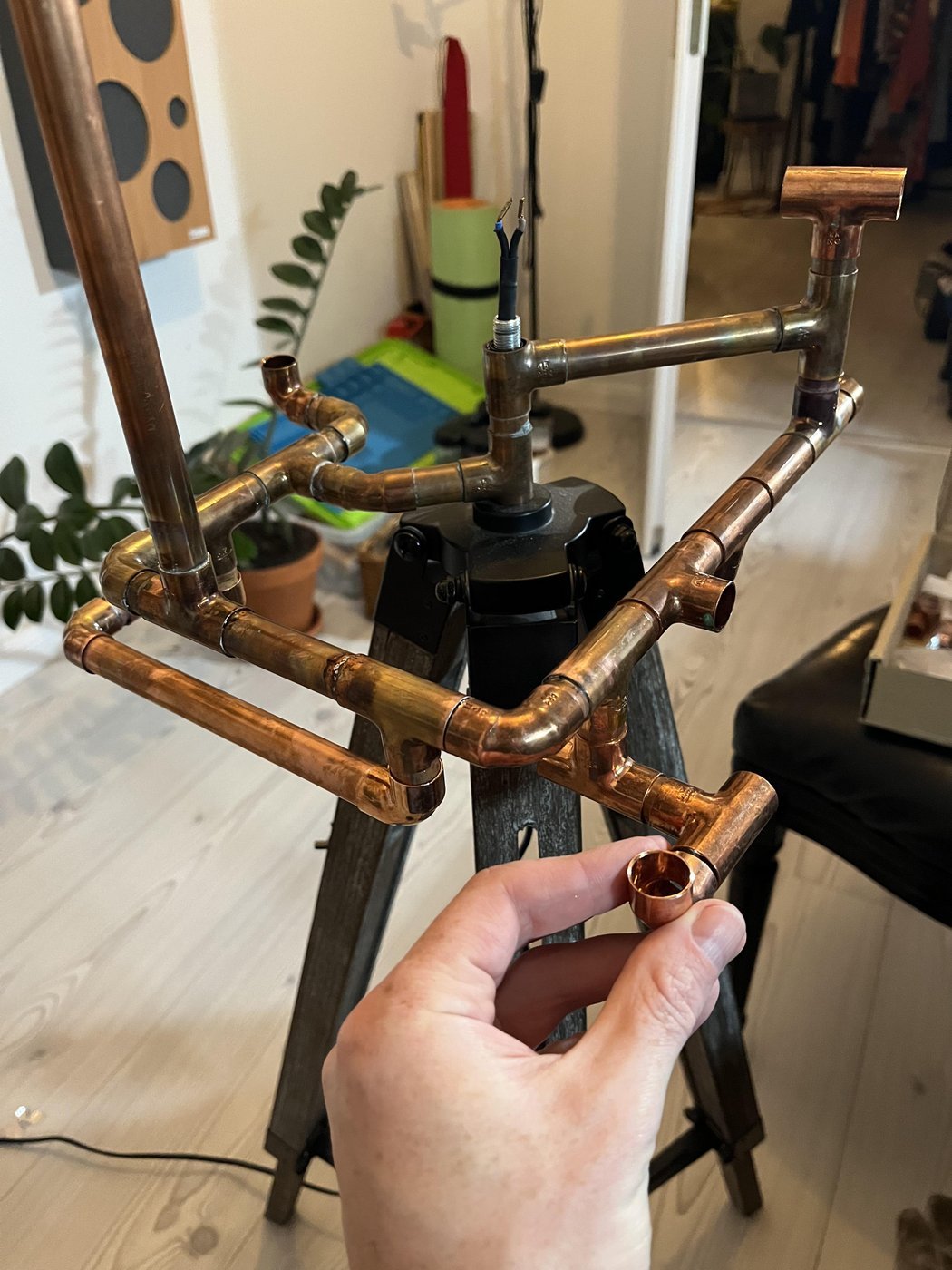
Второй проблемой было рассчитывать длины всех отрезков и чтобы получился ровный параллелепипед. Для этого сделал небольшой скетч в тетрадке и высчитал базовые размеры трубок. Скетч не сохранился, но он особо и не помог тк заводские тройники и уголки имеют разную глубину входа трубок и как бы я не вымерял длину трубок, в половине случаев их приходилось подрезать по месту.
Трубы резал специальным резаком:
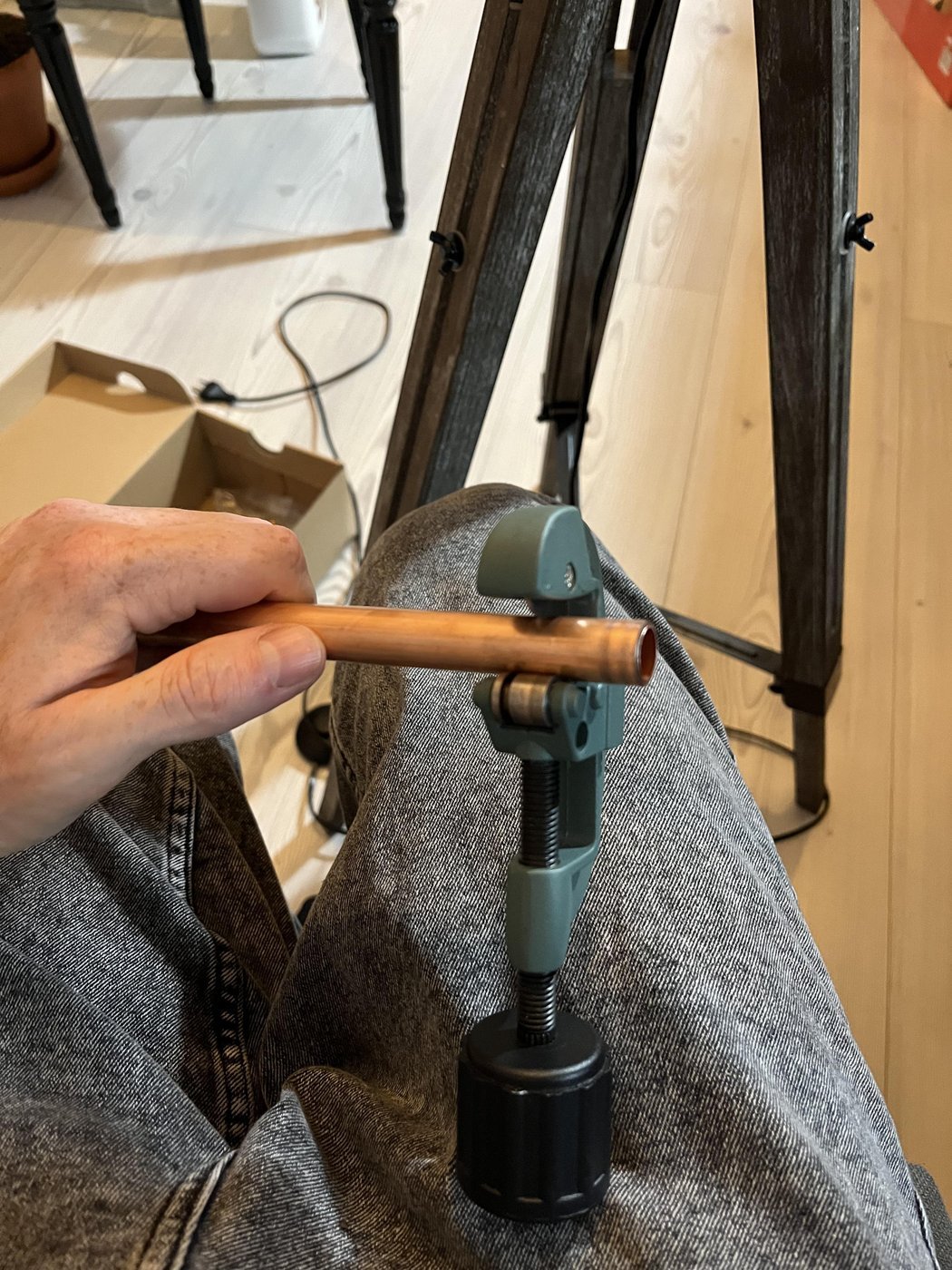
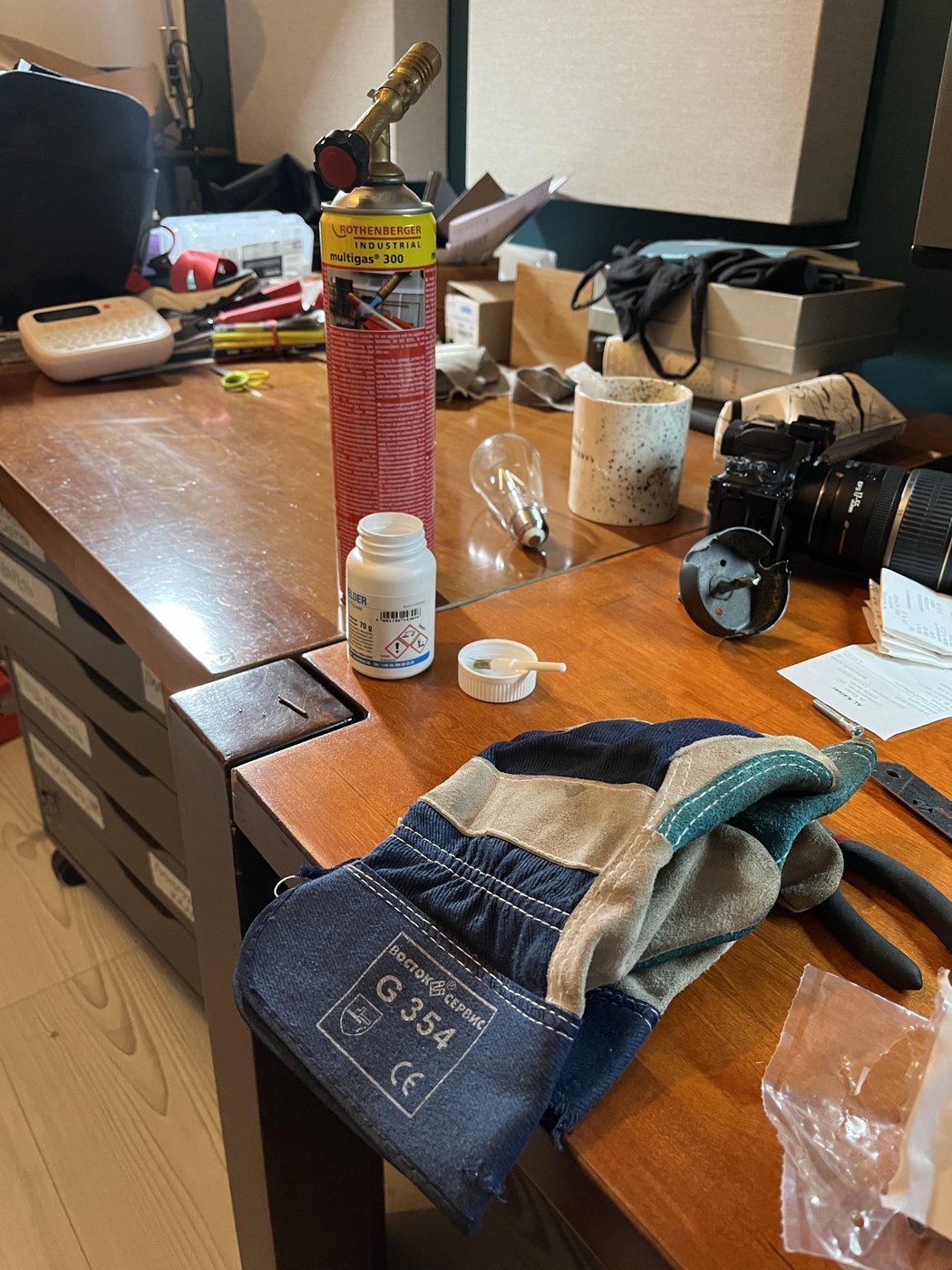
Потом паял горелкой с оловом:
Ушло 10 метров трубы и 150 уголков и тройников.
Tips&tricks
Смоделируйте всё в каде перед началом
Пайку наверняка можно заменить на клей
Закупите материалы онлайн, тк у вас всё в каде вы будете знать "сколько вешать" и скорее всего сильно сэкономите.
Используйте защиту, я паял в сварочных рукавицах, плотных джинсах и рабочей обуви.
[upd]
Чуть не забыл фотку с логотипом!
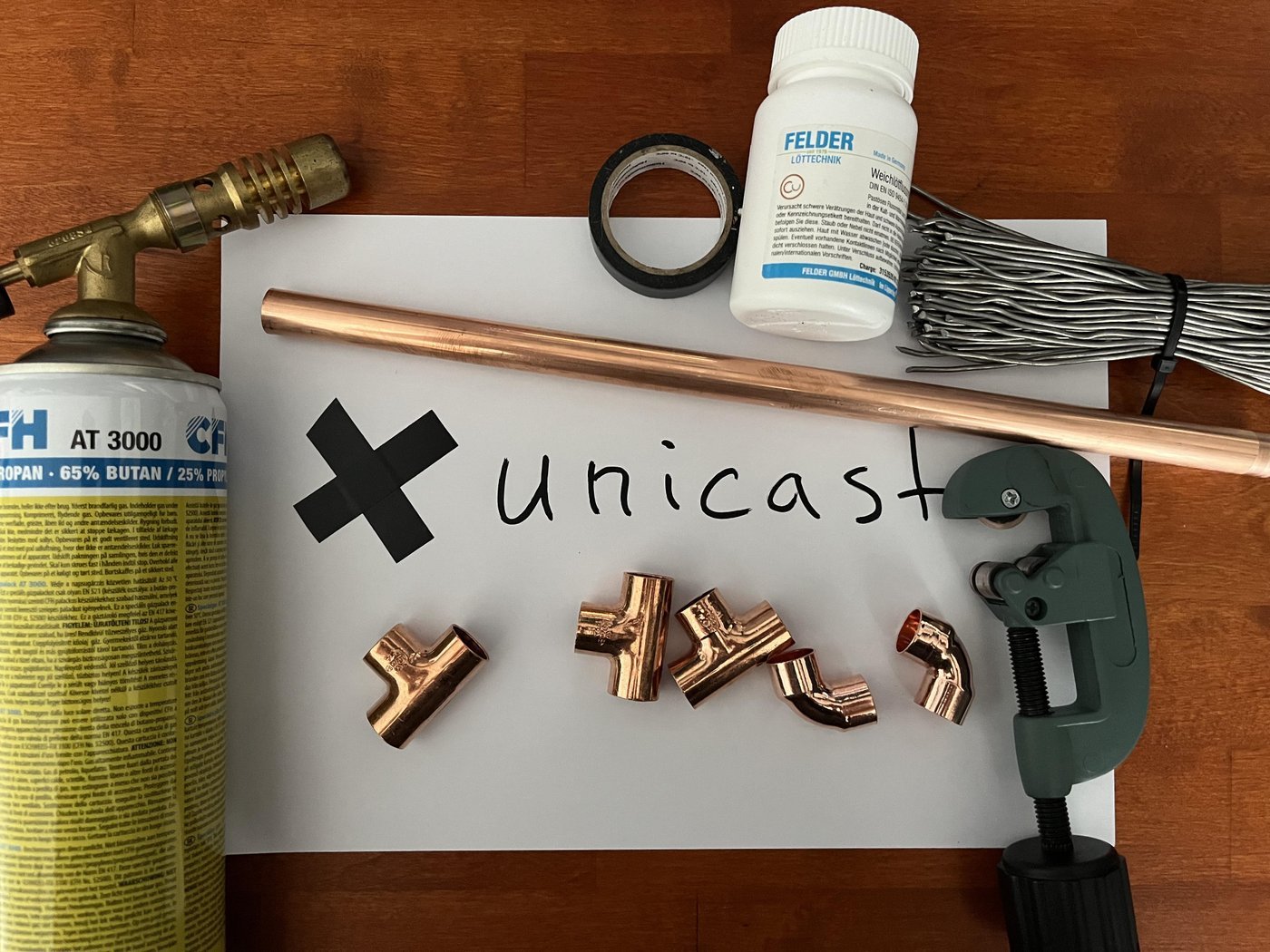
Самоделка: Менажницы из ясеня
Фото результата:
Раньше я работал на мебельном производстве, и по достижении определенного опыта мне стали приходить в голову мысли: "А почему бы не сделать что-то прикольное для дома?" Так я и сделал много разных вещей, хотя редко снимал этот процесс.
Следующие фото и видео были сняты просто для себя, чтобы показать жене и друзьям. А теперь, увидев этот пост, решил поделиться и с вами. Возможно, кому-то будет интересно!
Зачем я делал эти менажницы? Наверное, просто потому что мог 😄 Конечно, снеки можно было бы выложить на обычную обеденную тарелку или купить менажницу из фанеры за 500 рублей на Ozon.
Но, видимо, тяга к прекрасному побеждала😄!
Всё, кроме покрытия, делал сам.
Описание процесса:
От одного из заказов оставалось два кусочка щита из ясеня примерно 400х400х40 мм, решил сделать себе менажницы, видел их на маркетплейсах, но там у них была маленькая глубина и не нравились расцветки
Эти щиты были после работы на ЧПУ, из них уже вырезали ножки для каких-то хитрых кресел, сначала я отторцевал их на форматно-раскроечном станке в нужный мне размер, чтобы не носить лишнее и было проще крепить на стол
Накидал чертеж, написал программы для станка
Закрепил к столу станка с ЧПУ и начал выполнять различные манипуляции
Первая программа – 11 мин – черновой проход, компрессионная трехзаходная фреза d10 мм. Сразу по хардкору(всё происходило после работы, штуку, конечно, хочется сделать аккуратно, но и домой тоже хочется😄), на 32 мм глубины, шаг сдвига 5 мм. Звуки адские, ни скорость подачи, ни регулировка оборотов шпинделя ничего толком не дали. У ясеня и берёзы вроде бы не большая разница в твердости, но на берёзе такого звона никогда нет(бывало и такое, что отвернулся,неправильно написали программу станок заглючил, и перерезал 40 мм щит поперек на всю глубину за раз🤣).

Вот такая фреза
Ну да ладно, и так сойдёт – главное, что результат норм
Видео с процессом:
https://youtube.com/shorts/xYbvIhIY-9E
Вторая программа – 1 ч 11 мин – "чистовой" проход, фреза концевая d6 мм с круглым торцом(вообще она для алюминия и меди, но тут тоже отлично справилась). Тут уже всё происходит аккуратней, основное количество ненужного материала уже сфрезировано. Скорость подачи та же, шаг сдвига уже намного меньше, точно не помню, около 2 мм. Была опасность, что фреза вывалится из "патрона", т.к. общая длина фрезы 50 мм, а ей нужно заглубиться на 36 мм в заготовку + нужен запас по высоте от заготовки до зажимной гайки шпинделя + гайка выступает мм на 3 от цанги, цилиндрической штуки , которая и держит фрезу в патроне, его мощность 5,5 КВт и он не остановится, а будет просто гайкой жечь заготовку. В общем, фреза держалась за хвостик 8 мм, это очень мало и капец как неправильно, но
мне повезловсё прошло нормально😄Видео с процессом:
https://youtube.com/shorts/g3PYWb5C8RQ
https://youtube.com/shorts/HmjhQzzKjxo
Выглядит уже намного лучше
Третья программа – 2 мин – еще разок меняю фрезу, ставлю обратно d10 мм как на первой программе. Вырезание детали по кругу, фреза всё время опускается, за один круг на 5 мм. Без "перемычек", эта фреза удаляет стружку вниз, т.о. забивает её в пропил за собой, в конце немного придержал деталь рукой для подстраховки т.к. глубина прохода небольшая и стружки не сильно много(фанера 20 мм такой фрезой режется за один проход и всё отлично держится)
Видео с процессом:
https://youtube.com/shorts/RQcMlVmLSX4
На этом работа с ЧПУ была завершена.
Дальше меня ожидала "увлекательная" шлифовка, всевозможными машинками/станками/руками
Затем в малярке покрыли белой морилкой и пищевым лаком.
Ну а результат на фото вверху)
Tips&tricks:
Кайфуйте пока кайфуется от чего кайфуете 😅
p.s. Подскажите кто-нибудь как встроить видео в комментарий, пожалуйста. Через HTML iframe чет не получилось
Отображалка подписчиков на ютубе.
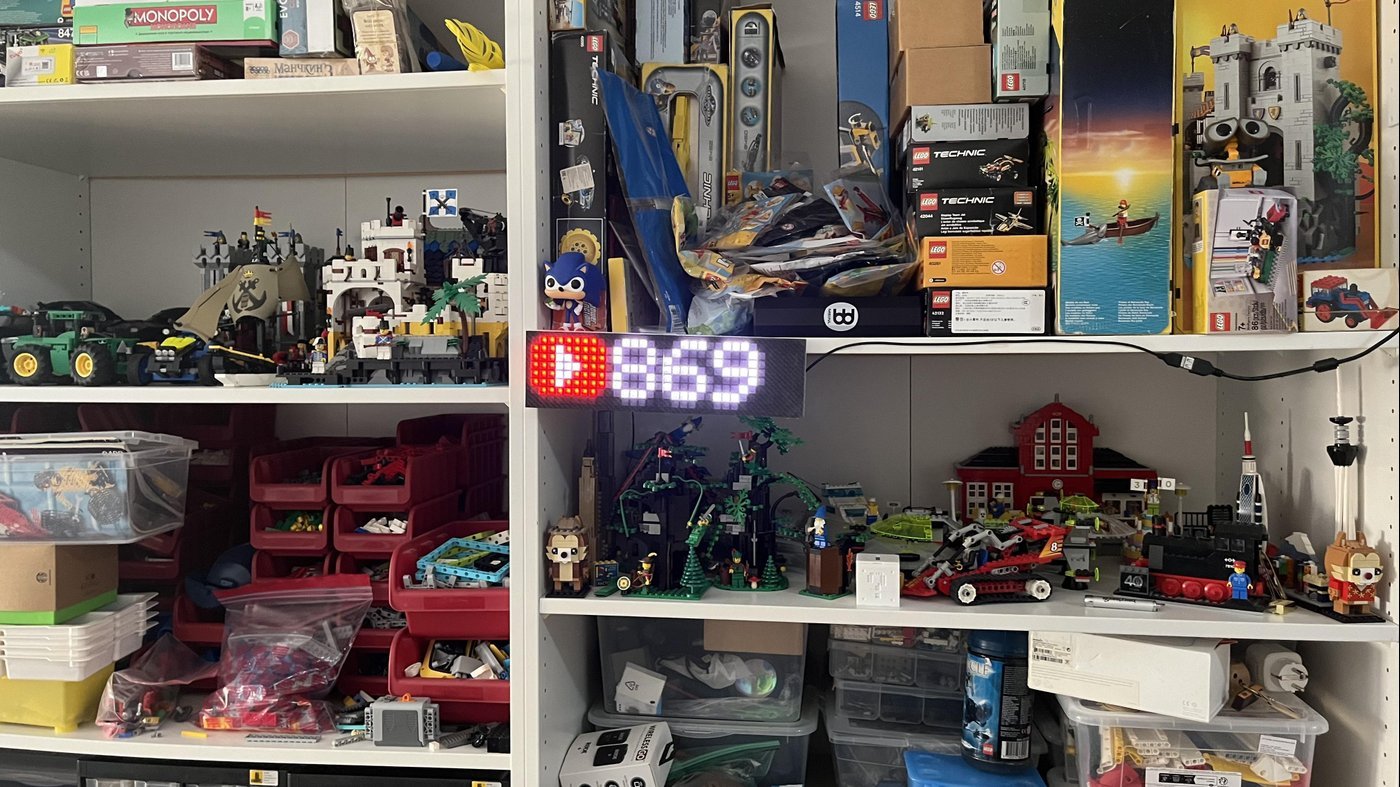
В живую выглядит чуть приятнее чем на фото - не так сильно видна засветка в смежные пиксели.
Все, включая диффузор - печатал на принтере. Из не печатного только матрица ws1228b и esp32 плата. Собрано на термосопли. Не стал делать хорошо - был высок риск, что будет валяться в ящке недоделанным.
Самоделка: полки для противней
Проблема которую мы решаем
Купили мы значит электрогриль от Tefal(спасибо кухонному чатику за это). Tefal думает о нас, не пригорает, но не думает о том где и как нам теперь хранить его съемные панели. Место нашлось только на полке с противнями и решеткой для духовки, но было не очень удобно. Примерно полгода меня это по чуть-чуть подбешивало каждый раз когда нужно было что-то, и вот наконец надоело совсем.
Фото результата
Описание процесса
Скребем по сусекам, ищем в кладовке остатки стройматерилов. Нашлись обрезки доски 44x67мм. Измеряем противень и решетку, и выбираем пазы вдоль всей длины доски.
Ответная часть крепится не сбоку(усилие на сдвиг), и сверху(усилие на отрыв), поэтому я чуть-чуть подрезал ее, чтоб весила поменьше.
Есественно пазы в обоих частях одинаковые и на одном и том же расстоянии.
Потом я купил 3М’овский двусторонний скотч, не все удалось наскрести по сусекам.
и вуаля, вот вам маленький stop-motion видосик результата
Tips&tricks
Самоделка: раскроечный стол для жены
Размер: 1 х 1,8 м. Разборный: иначе в комнату не занести.
А зачем оно надо?
У жены есть хобби - шить одежду. Это футболки, платья, худи. Шьёт только нам или друзьям. Раньше она делала это дома, на полу. Жутко неудобно, всюду обрезки и иглы... Сняли небольшое помещение, отвезли туда все её "игрушки". Нужен стол. Такой, чтоб со всех сторон подойти можно было и чтоб по высоте достаточно, и чтоб здоровенный был.
Процесс создания
В гараже как раз валялся профиль 30 х30. Из него сделал ножки и верхний периметр длинных боковушек.
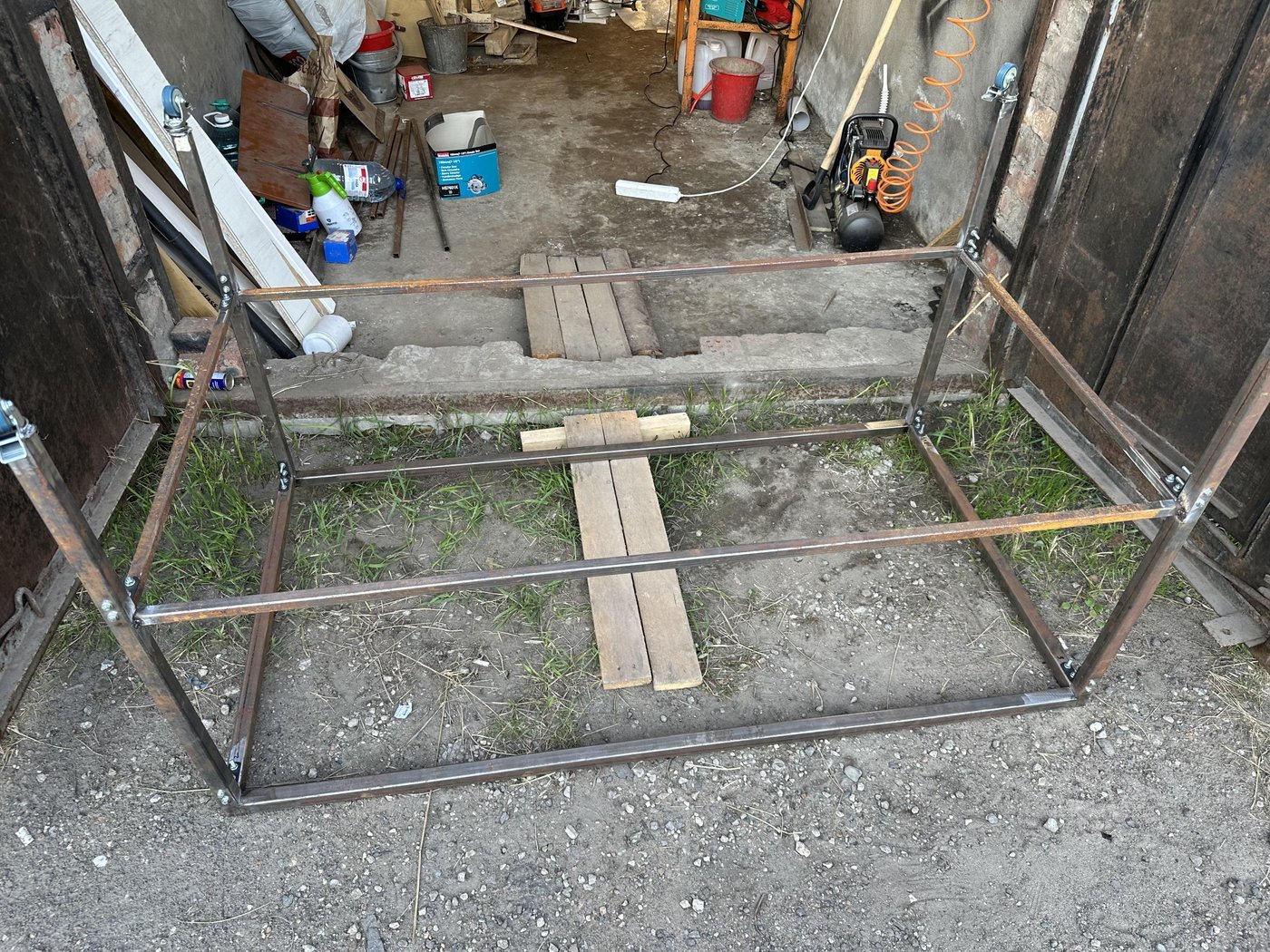
Нижний контур и перекладины короткой стороны из профиля 20 х 20. Короткие стороны собраны на болты м6 и какие-то уголки из леруа.
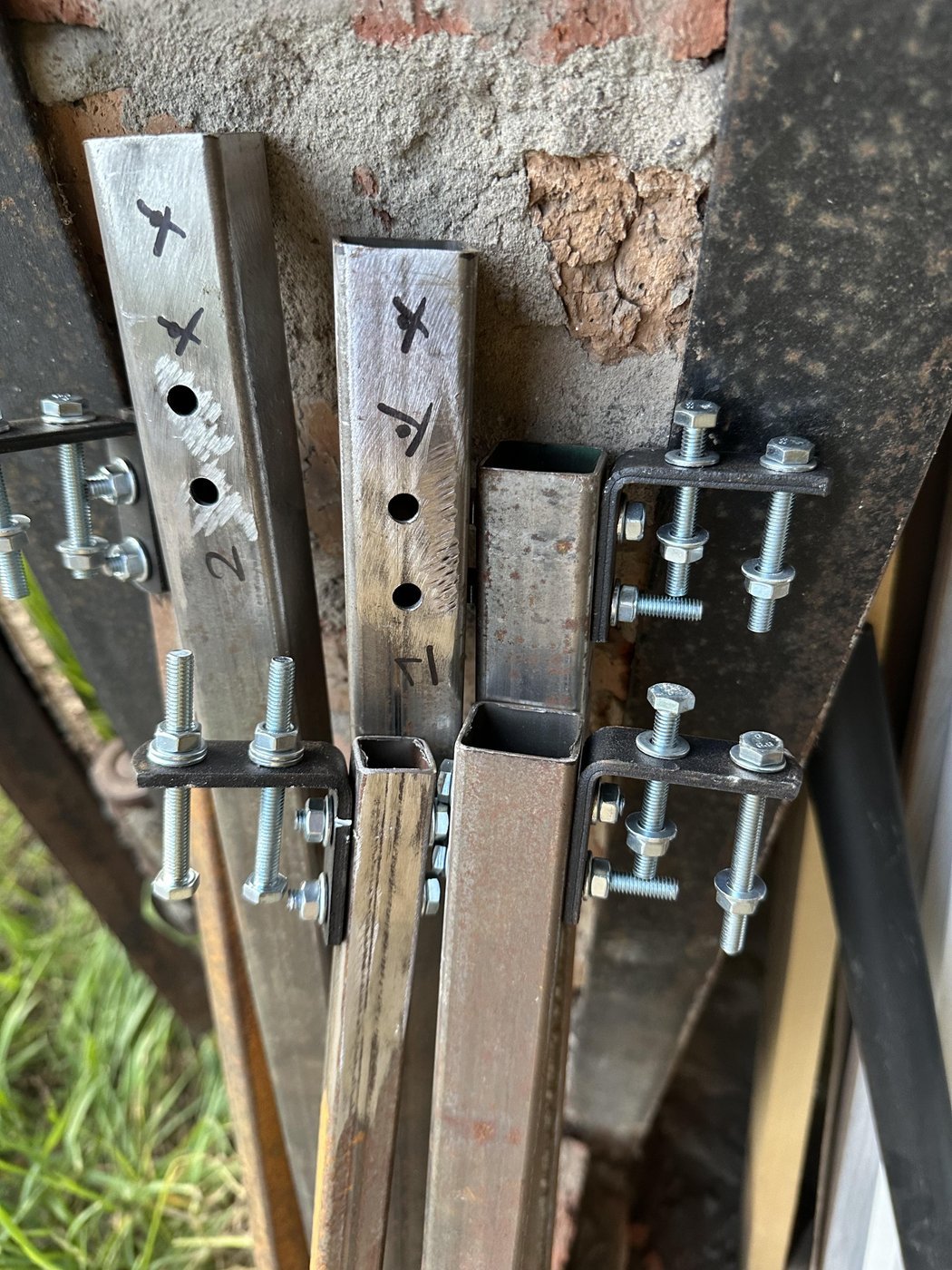
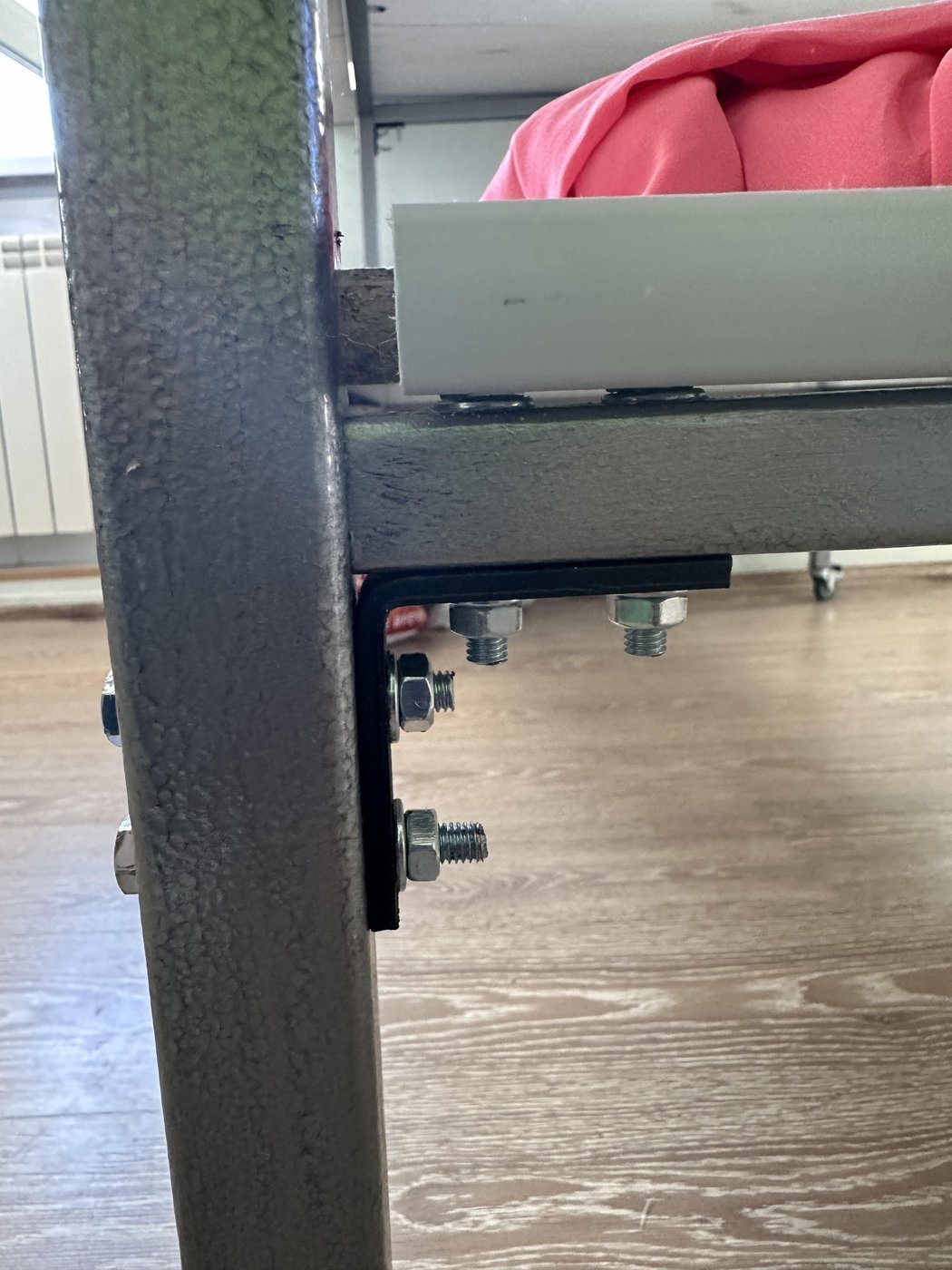
Колёса с фиксатором из леруа, на подшипнике. Искал способ сделать их съёмными, но зачем их снимать если с ними удобно. Приварил наплёвками.
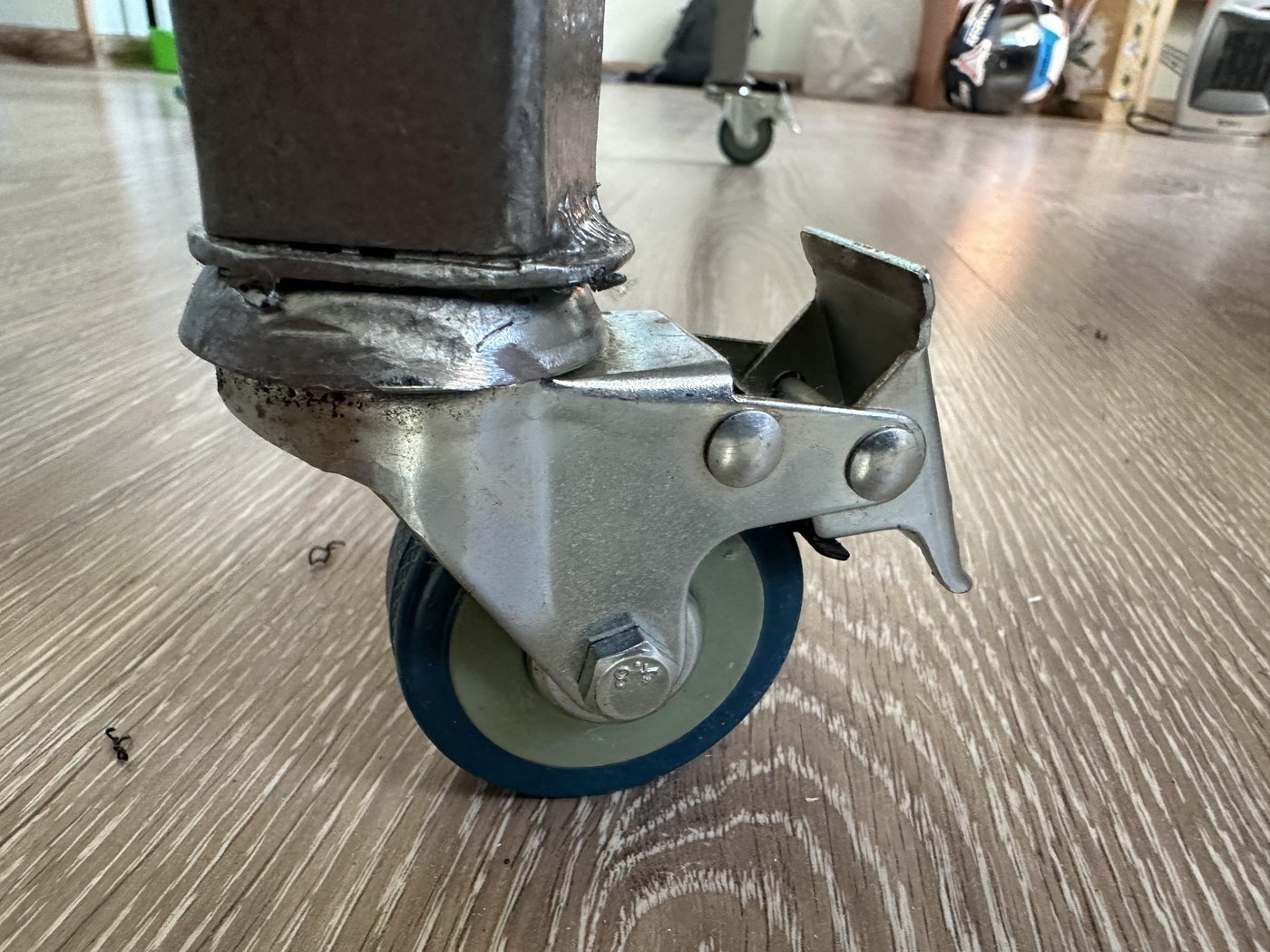
Мои "швы":
Каркас окрашен молотковой краской в 2 слоя.
Столешница: Плита ЛДСП
Кромка закрыта спец полосками из леруа, они просто надеваются плотно, ничем не склеяны.
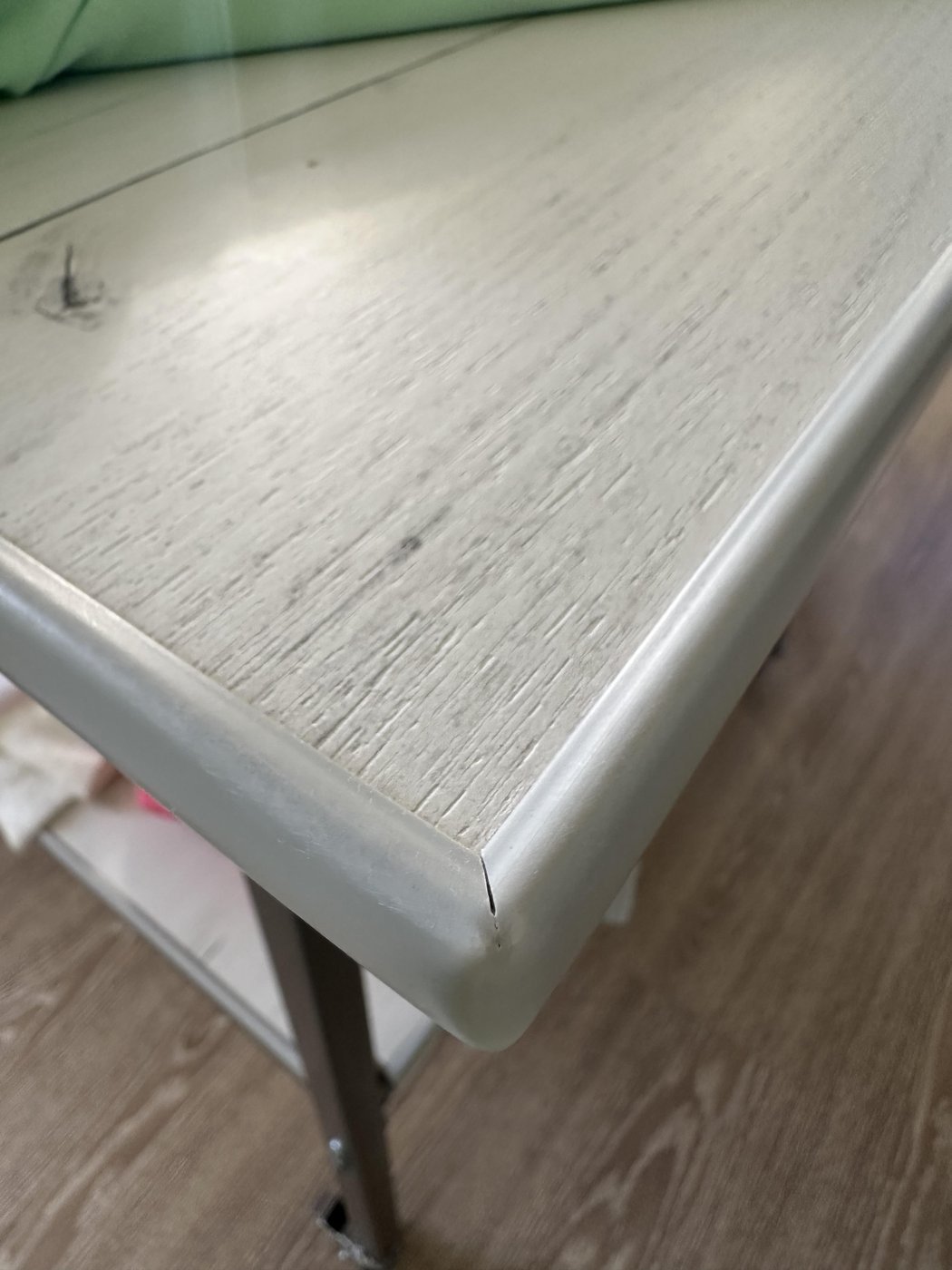
Итог:
Потратил дня 3 итого, но они были размазаны на 2 месяца из-за погоды: то дожди, то жара +239. Себестоимость проекта примерно 7000 российских рублей.
Tips&tricks
Coffee table (или журнальный столик)
Первый проект материал для которого я прям купил-купил, а не залутал с помойки/притащил пень из лесу. Планки из European Oak , и дубовый мебельный щит.
Фото результата
Описание процесса
Если честно, в этом проекте мне хочется уделить больше внимания не описанию процесса, а тому где/как можно обосраться в процессе, и как этого не сделать(или как исправить если сделал). Но так и быть пару фото процесса у меня есть:
Ножки собирал на half-lap joint(+ шканты), глубину выбирал кромочным фрезером - сойдет, но это не самый подходящий для этого инструмент
Вот ножки уже собраны, но еще не обработаны.
Вот тут наверное лучше видно шканты и half-lap joint ножек
Подстолье крепится к столешнице 4 винтами, винты вкручиваются в футорки
К поперечной царге(палка между ножками) крепление такое же: винты + футорки. Очень хотелось сделать все разборным, не знаю зачем.
Все что можно торцевал радиусной резой 6мм, поверх покрывал масло-воском.
Tips&tricks (где можно обосраться)
Мебельный щит
Если влажность в месте где ваш мебельный щит был изготовлен, в месте где он хранился в магазине, в вашей мастерской и в вашей квартире отличаются друг от друга, то мебельный щит, массив же, не какая-то плебейская фанера 😍, может сделать так:
То есть принять форму вот этой скобочки)
К счастью, внутри квартиры влажность его устроила больше, и щит попустило до состояния |
Футорки-винты
Так как это соединение жесткое, а мы не хотим чтобы все наши труды пошли коту под хвост одним сухим летним днем или влажным зимним, нужно заложить люфт(примерно 1% от размера щита).
Поэтому винт здесь М6, а отверстие под него 8 мм. Но это я не сам такой умный сразу все продумал, это мне в DIY'ном чатике посоветовали, за что им большое спасибо ❤️❤️❤️
Футорки
Так как стол хотелось бы иметь ровный, то нужно сверлить отверстия под винты и вкручивать футорки нужно строго под 90° к поверхности.
Поэтому рекомендуется озаботиться кондуктором(предъявите билетики👩✈️) для сверления под прямым углом, и потренироваться на каком-нибудь не очень нужном брусочке.
Вкручивать футорку рекомендуется также через кондуктор(я сразу накрутил на винт), потому что даже в перпендикулярное поверхности отверстие футорку можно вкрутить не перпендикулярно, увы
Винты
Хочешь красивую плоскую шляпку под шестигранник? Добро пожаловать, такие винты у нас начинаются от М6 и от 60мм. Поэтому встречайте, слева-направо:
Подставка под запястья для механической клавиатуры
Ввиду появившегося в этом году туннельного синдрома и болей в спине, начал работать над эргономикой рабочего места. До этого два года работал буквально на laptop'е (на диване на коленках с ноутом). Купил мышку, подставку для ноута чтобы экран повыше был, новую клавиатуру (Keychron K8 Pro). Но после многих лет низкопрофильных ноутбучных клавиатур она оказалась нереально высокой, держать руки на весу продолжительное время некомфортно, поэтому понадобилась подставка.
Фото результата
Описание процесса
Подставка распечатана на 3d-принтере из PLA. В другое время сделал бы из массива дерева, но мастерская моя с инструментами и материалами осталась в прошлой жизни.
Модель с плюс-минус подходящим дизайном нашел на Thingiverse, подредактировал под мои размеры в Fusion360. Целиком в мой принтер она не влезла, поэтому печатал из двух частей с соединением на ласточкин хвост (все-таки вплел столярку, хех).
Для экономии пластика и времени подставка внутри полая, думал может залить внутрь эпоксидку для увесистости, но пока не нашел, где взять, да и в целом на функциональность никак не влияет.
Наверх для стиля и более приятных тактильных ощущений наклеил натуральную кожу.
Tips&tricks
В качестве противоскользящего материала на дно наклеил простой советский... синюю изоленту. Резину надо искать где-то, а изолента всегда под рукой, и под весом рук ПВХ (материал из которого она сделана) оказался достаточно устойчивым.
Для вырезания кожи по форме сделал сначала шаблон из бумаги, примерил, подправил где надо. Если отрезал от шаблона лишнего, чтобы не переделывать заново, можно просто подклеить на проблемное место новый кусочек бумаги и попробовать еще раз.
😱 Комментарий удален его автором...